Everyone’s going wild for supply
Supply chain is moving from the backroom to the boardroom. Because if you can’t get your product to your customers, what have you got?
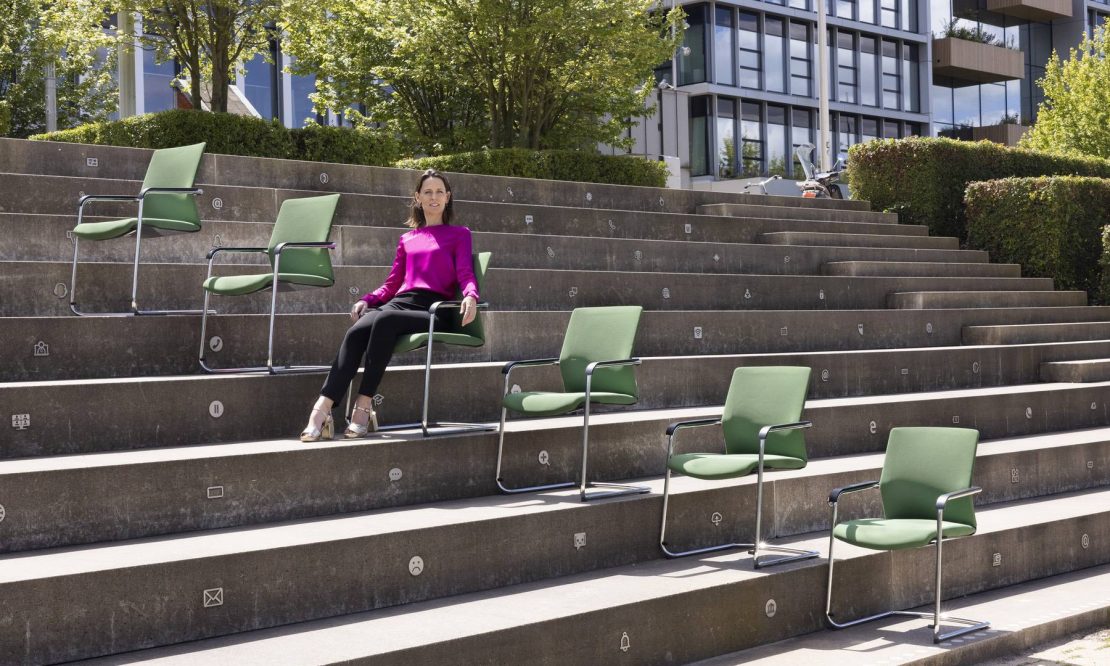
Marketing smarts? Ten a penny. Finance bod? Meh: the quants are queuing up. But supply chain expertise? The C-suite crowd is going wild for you guys – because if you can’t get your product to your customers, what have you got? From a global pandemic to the Ever Given container ship stuck in the Suez Canal, from trade wars to actual wars, the last few years have put supply chain front and center. Businesses have learned the hard way that the unpredictable happens all the time, and that their supply lines are much more fragile than they thought. That’s why supply chain professionals are moving from the backroom to the boardroom – and fast.
“Covid shone a light on the importance of supply chain that businesses simply hadn’t grasped before,” says Dr. Merieke Stevens, Associate Professor of Technology & Operations Management. “There was an assumption within industry that supply chains just worked. The markets would ensure that if you organized your first-tier suppliers well, you didn’t need to worry about your second or third tiers, because every organization in the network would take their responsibility for their direct partners. People thought that if somewhere, deep in the chain, there was a problem with getting products that are not technologically advanced – screws, nuts, bolts – they could easily switch suppliers. They learned during Covid that that’s not true.”
As a result, thousands of businesses are not just recruiting more supply chain experts but ensuring they are integral and board-level. Those professionals will need to deal with big new issues. Dr. Harwin de Vries, Associate Professor of Technology & Operations Management, believes industry can learn much from the supply chain management practices of humanitarian organizations.
“Business became so obsessed with cost that it evolved to a ‘just-in-time’ supply. This becomes a problem if applied when a supply chain is still subject to major uncertainties and risks,” he says. “Companies took the slack out of production and out of inventory – it was cheaper to rely on one supplier, even if that supplier was thousands of miles away with several links in the chain. There was no backup – but because things had been relatively calm for a couple of decades, many companies were less concerned about the risk.”
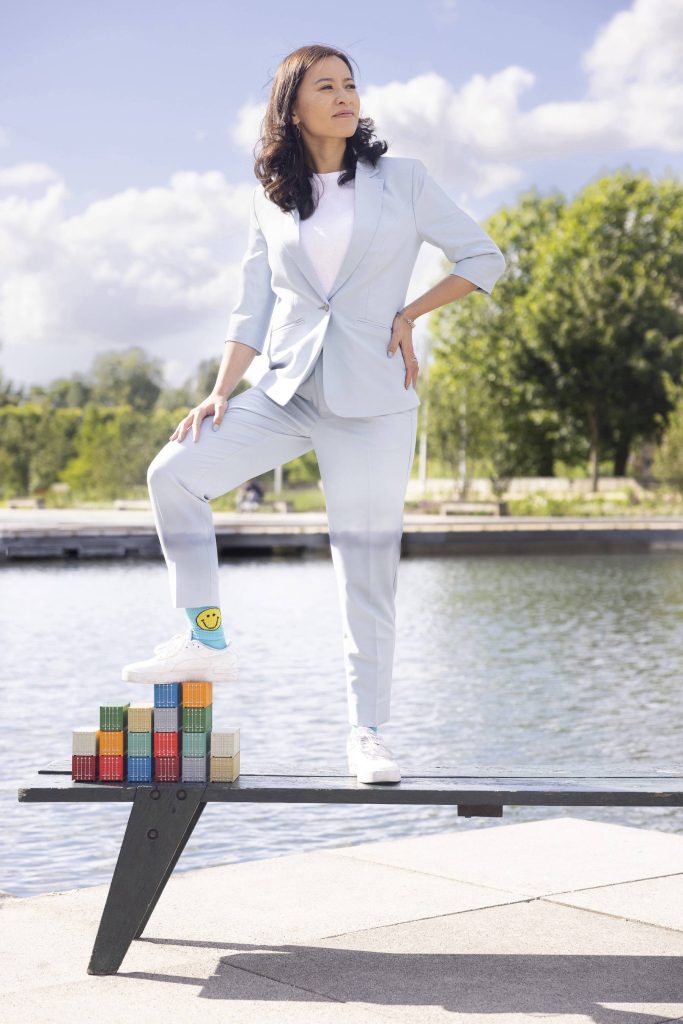
Then came Covid – and the disruption was familiar to humanitarian organizations, which have prepared supply chains to ‘jump in’ when a disaster creates a demand-side or supply-side disruption. “The humanitarian organization then quickly scales up a supply chain to fill the gap. They are thus essentially playing the supply chain risk manager for populations that may get hit by a disaster in the future,” de Vries points out. “But they also have a very comprehensive approach – for example, training people to effectively deliver a response, optimizing coordination mechanisms and roles and responsibilities during a response, and by investing in information management systems that help them during the response. They also preposition inventories in warehouses close to disaster-prone areas and maintain a database and framework agreements with local suppliers.”
Businesses could learn much from this approach, he says – and, indeed, the commercial sector is enhancing its focus on supply chain risk management. “Businesses are, for instance, increasingly considering multi-sourcing, reshoring, near-shoring, and ‘just-in-case’ inventories to make supply chains more resilient – though some are far more serious about this than others.”
Take, for example, the growth of the south-east Asian fast fashion market. It’s enabled companies to source more and cheaper products from further away – but with little control over what happens in the deep tiers of the supply chain. Customers demand speedy delivery, pressurize companies to cut corners, then publicly shame them for opaque, unethical, and unsustainable supply chains.
“There’s an expected sense of responsibility that wasn’t there ten years ago,” says Stevens. “Back then you might get one or two people concerned about exploitation. Now, it’s a big issue with younger people in higher-income countries.” However, she says, many companies aren’t being deliberately oblique about their supply chains: they probably don’t know the full picture themselves. “Many wish they did. But the reality is, they may outsource something to a supplier who may not have the capacity and has to go round the corner to their cousin and have them make it. Not only will the final customer not know, nor will the company that’s buying it from the supplier. There is a lot less transparency and visibility than anyone would like.”
But having a supply chain that visibly ticks all the right boxes can also bring its own problems, adds Stevens: if companies go beyond in terms of compliance to be seen as more sustainable, their competitors may offer something cheaper. “And there are still too few people in this world who have the bandwidth to buy sustainably,” she says. “That makes it hard for a business to survive in the market by doing every single thing right.”
So what does your company need from its 21st-century supply chain professional? Global supply chain managers of the future will need similar core skills to the ones they’ve always had – but enhanced for this new world. “Risk management is obviously key,” says Belina Do (MSc Supply Chain Management, 2016), a freelance IT and supply chain consultant. “The integration of data and technology in risk management is not just beneficial but essential. Real-time visibility enables quick decision-making and proactive problem-solving.”

Supply chain managers need to understand what their data means, where there could be a problem and how to mitigate that risk, Do points out. “But to do that you also need soft skills: to communicate, to collaborate, to problem-solve and to take your colleagues and partners with you. These skills need to be broad because every new problem will differ from the last.” Because what’s really changed, says Stevens, is how we conceptualize supply chains. “What happened before was a chain of events that wasn’t embedded. Now we’re moving towards seeing supply chain as an embedded ecosystem, where every single person fits a particular role.”
Getting those skills right, says de Vries, results in good risk management that gives you a competitive advantage – as demonstrated by Toyota during the pandemic. “It took the loss of just one type of component – the semiconductor – to halt the entire motor production line of almost all car manufacturers,” he says. “But Toyota had learned from the disruption following the Fukushima earthquake and tsunami of 2011. They’d agreed with their suppliers to keep a certain minimum inventory of every component critical for production. They combined efficiency with adequate risk management, and that planning really benefited them during Covid. Toyota spent decades investing in, communicating with and co-ordinating its supply partners. Supply chain management can be the difference between huge success and huge failure.”
That’s why, he says, companies need to think of supply chain risk management not as a desirable add-on, but something embedded in their way of thinking – though that doesn’t mean being prepared for every eventuality. “That turns companies off anyway. They say, ‘every disruption is different, so how can we ever start mitigating the risks?’ But while companies can’t prevent everything, they can look at the broad consequences of certain types of risks. It’s about how you prepare roles and responsibilities, map out co-ordination with key stakeholders, and take a holistic perspective. Managing those risks requires a generic set of steps and strategies. Companies should not necessarily assess and mitigate each individual risk. If you’re prepared for big risks, you find that you’re often automatically prepared for the smaller ones.”
It’s a big mindset shift and companies will need to identify and overcome two powerful biases to think differently – particularly when everything is fine. “There’s the optimism bias: people think something bad is not going to happen to them,” says de Vries. “Then there’s the preparedness paradox: asking why you are investing so much in an eventuality that hasn’t happened, without realizing it hasn’t happened because you invested so much in preventing it.”
So, if your boardroom table is lacking a supply chain professional, take note. Just like most of the car industry during Covid, you’re missing a vital part of the chain. “Risk management around supply chain is becoming a necessary and embedded part of company culture,” says de Vries. “Businesses are understanding that supply chain needs to sit within its whole strategy. And they’re employing professionals that can help make it a core focus.”